Concrete Milling 101
Have you ever driven down a particularly smooth highway and noticed all the parallel grooves running in the pavement? Those grooves are the result of effective concrete milling.
Concrete milling is a process that strips layers of concrete from roads, bridges, parking lots, and other paved surfaces to create a smooth surface with plenty of grip.
Even though concrete surfaces that have been milled are finished and level, they need maintenance over time, in order to make sure they’re safe and well-cared for.
This maintenance is carried out to make sure the concrete surfaces stay within regulation for roads, bridges, sidewalks, etc. A lot of equipment is involved in the concrete milling process, from the initial work to maintenance jobs.
Concrete milling equipment varies greatly in terms of size, function, purpose, and workload capability. To help you understand concrete milling equipment and what it’s used for, we’ve assembled this helpful “Concrete Milling 101” guide!
Why is Concrete Milling Done in the First Place?
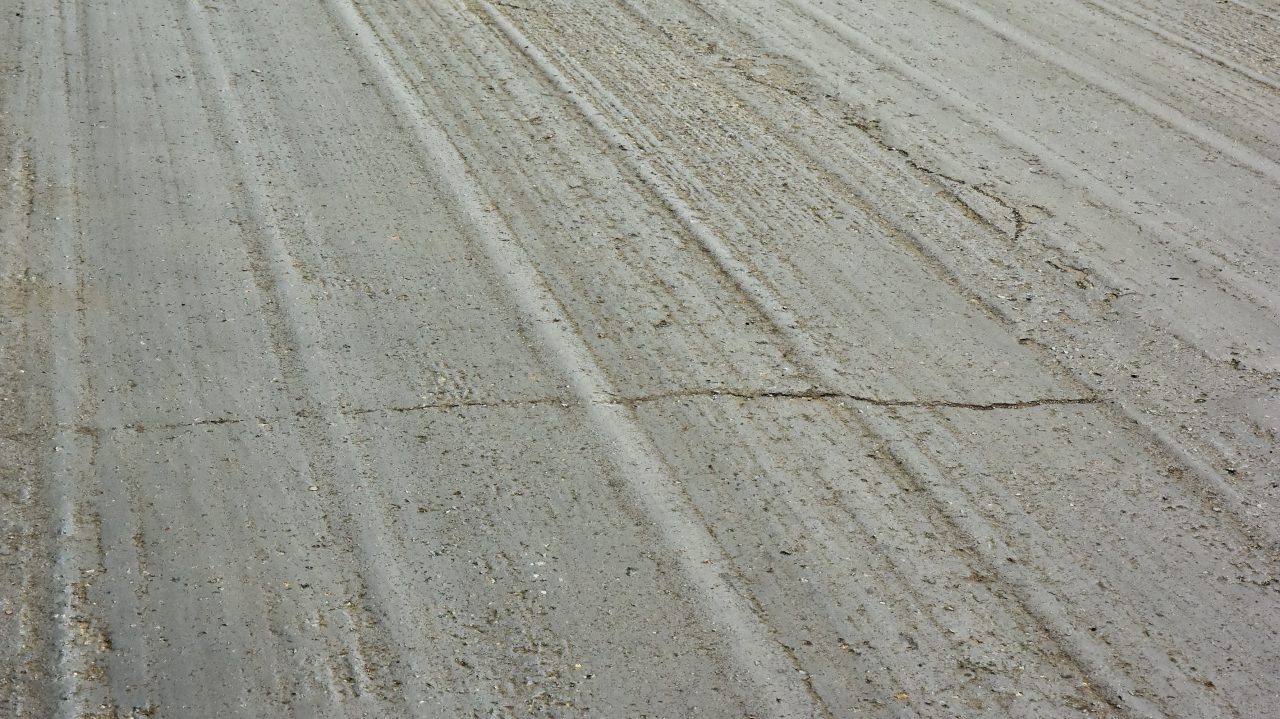
Concrete milling is done to fix irregularities in concrete and create a smooth, level surface that provides plenty of traction.
Why is this important?
Irregular or uneven concrete surfaces are unsafe for vehicles and pedestrians. They can result in tripping hazards, poor tire traction, and other hazards.
Milling helps to restore smooth concrete surfaces, preventing the previously mentioned safety hazards that could occur on roads, bridges, highways, etc.
Concrete milling also improves the functionality of concrete surfaces for vehicles, by minimizing conditions that result in screeching tire noises that are both irritating and harmful to tires. This results in an overall better road experience.
Not only does concrete milling help with road safety, but it’s also a great way to increase the visual appeal of concrete surfaces.
Milling grinds the upper surface layers and makes them look more appealing by removing oil stains, grease spots, and other debris.
Concrete milling is also helpful for carrying out waste-minimizing resurfacing projects!
The process of concrete milling creates reclaimed pavement material. This reclaimed waste product can then be recycled as the aggregate for new pavement, which is incredibly cost-effective and environmentally friendly.
How Does Concrete Milling Work?
Concrete milling is very similar to concrete scarifying—the only difference is the material of the spinning blades that chip away at the concrete. Concrete scarifiers typically use carbide-tipped blades, while concrete milling involves diamond-tipped blades.
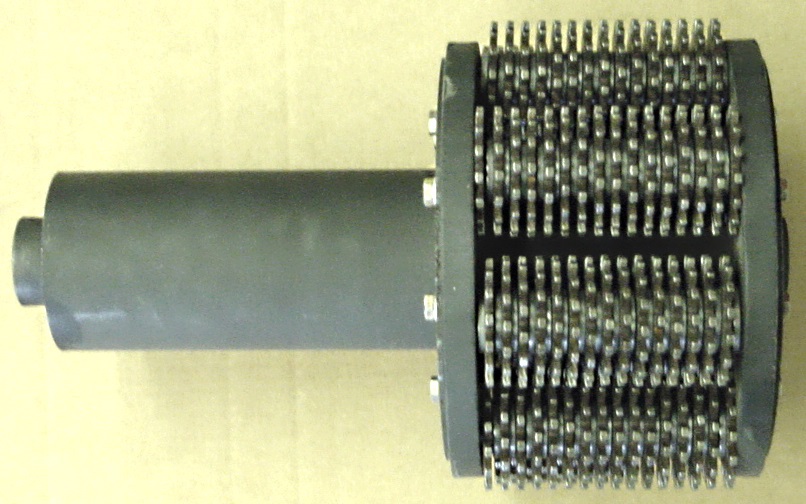
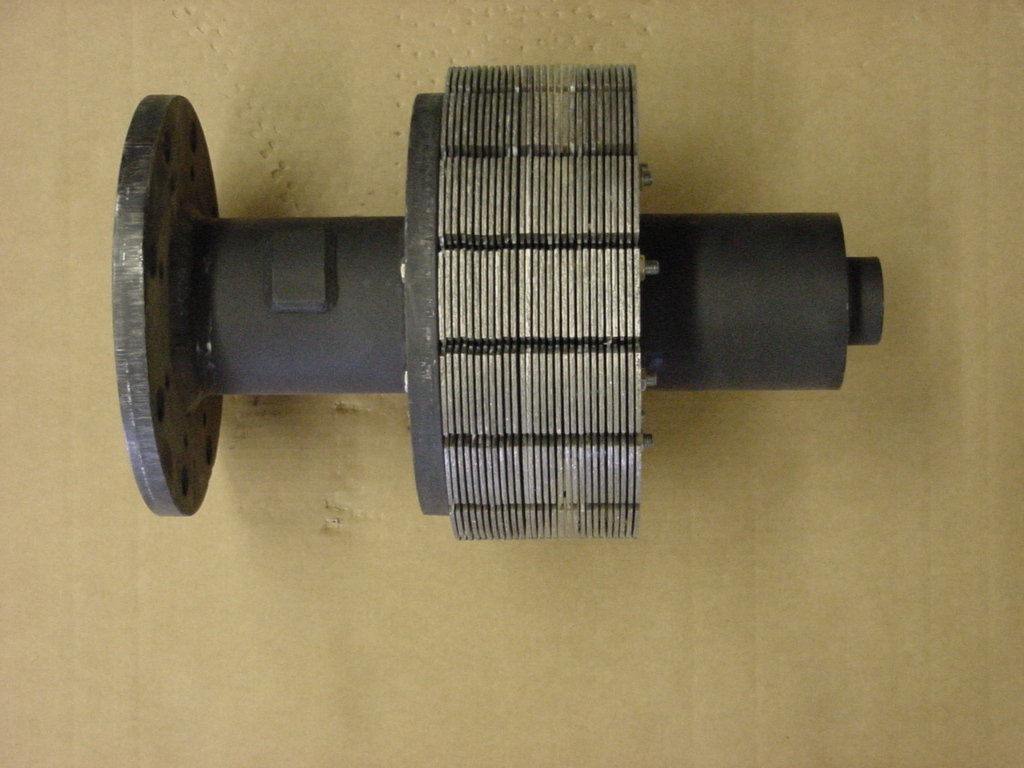
Concrete Milling Process
Concrete milling machines use diamond-tipped blades, attached to a rotating drum, that chip away at the top layer of a concrete surface.
These machines are great for heavy-duty concrete resurfacing operations, especially ones that involve chipping away a lot of surface material.
Milling machines carve distinct lines in the concrete, making the surfaces especially grippy for vehicles.
Similar to concrete scarifiers, concrete milling machines dig fairly deep into the concrete, scraping away up to ¼ of an inch per pass.
This means they’re especially useful for outdoor construction projects such as bridge construction and repair, road construction and repair, parking garage resurfacing, sidewalk and driveway resurfacing.
These projects often involve creating grooves in the concrete for traction or creating level spaces to get rid of tripping hazards.
Tips for Best Results in Concrete Milling
One of the best pieces of advice we have for concrete milling operations is to work at an efficient pace that balances productivity and quality control. It’s important to work quickly, but remember that rushing through the project can result in a lowered quality of work and even safety hazards.
Another tip we have is to pick a milling machine that matches the workload and end results of your project.
A major advantage that helps with concrete milling is having the ability to switch between milling and scarifying blades projects quickly. Our Multi-Purpose chassis makes this happen! Simply switch between our diamond milling cage or our carbide scarifying cage, and get to work.
The Multi-Purpose Chassis
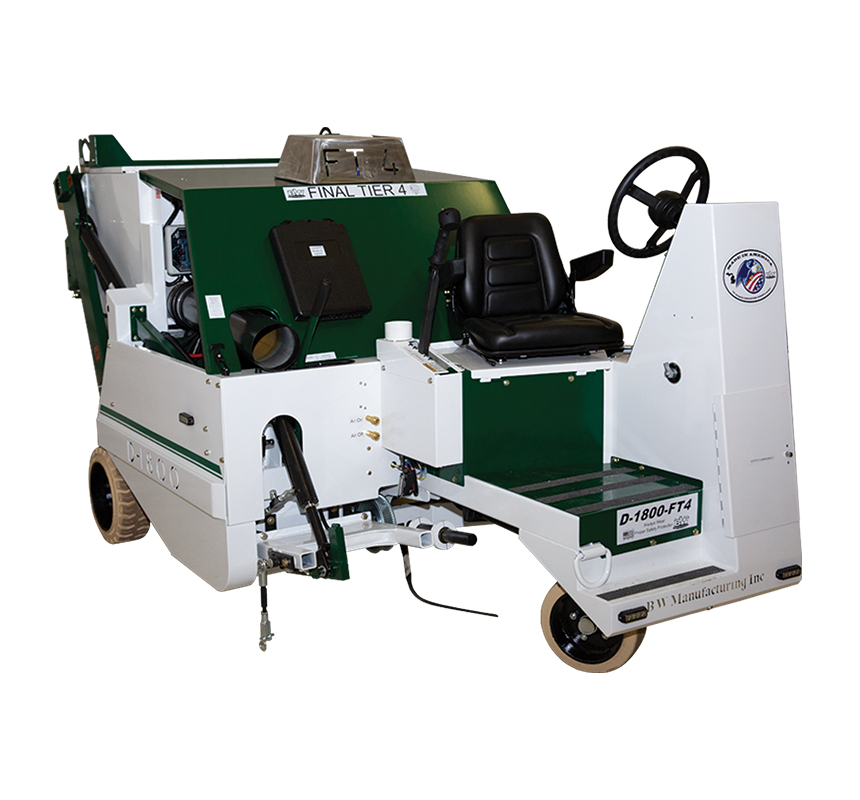
It’s so good that it demands a second mention. We are the only manufacturer with an all-in-one interchangeable chassis for your concrete surface preparation needs.
You’ll be shocked at how effortless it is to switch between scarifying and milling, shot blasting, and diamond grinding.
You’ll no longer have to wait for additional equipment to be delivered since you’ll have one machine that can handle it all.
With the Multi-Purpose Chassis, your business will finally have the power to execute tasks with multiple capabilities faster, and with great results.
Project management will become streamlined since you’ll be able to switch between scarification, shot blasting, and diamond grinding operations without bringing in new machines.
Your maintenance and repair costs will also be reduced, now that you’ll only need to maintain a single chassis, rather than multiple machines.
By saving you precious time and money, and improving your performance capabilities, BW Manufacturing’s equipment will empower you to bid for more jobs.
Want to learn more about the Multi-Purpose Chassis? Click the link and see how you could be doing your job better than ever before.
Conclusion
Concrete milling is the process of removing the top layers of a concrete surface. It’s carried out using scarifying machines equipped with diamond-tipped blades.
Milling operations are effective at creating level, smooth surfaces that provide a lot of traction. Plus, the material that’s chipped away can be repurposed for aggregate material later on!
As we mentioned, having a singular machine that can handle both diamond milling AND scarifying will make your concrete surface preparation much more efficient, saving you time and money. Our Multi-Purpose Chassis fills that need.
To learn more about how our Multi-Purpose and other concrete equipment can benefit your projects, visit the link below or contact us!