Distinguishing Surface Prep: Concrete vs. Asphalt Removal Techniques
When it comes to surface preparation, the approach and techniques used can vastly differ between concrete and asphalt surfaces. These differences are not just a matter of preference but are necessitated by the inherent properties and composition of each material. Understanding how the process varies can help professionals in the industry optimize their methods for each surface type, ensuring efficiency and effectiveness in their projects. This blog outlines the key distinctions in the surface prep process for removing concrete versus asphalt.
Understanding Concrete and Asphalt
Concrete is a composite material composed of fine and coarse aggregate bonded together with a fluid cement that hardens over time. It is known for its durability, rigidity, and resistance to compression, making it ideal for heavy-duty surfaces like industrial floors, highways, and building foundations.
Asphalt, on the other hand, is made by mixing aggregate with bitumen, a sticky, black, and highly viscous liquid binding agent. This composition gives asphalt its characteristic flexibility and waterproof properties, which are perfect for roads and driveways that need to accommodate temperature fluctuations and vehicle weights.
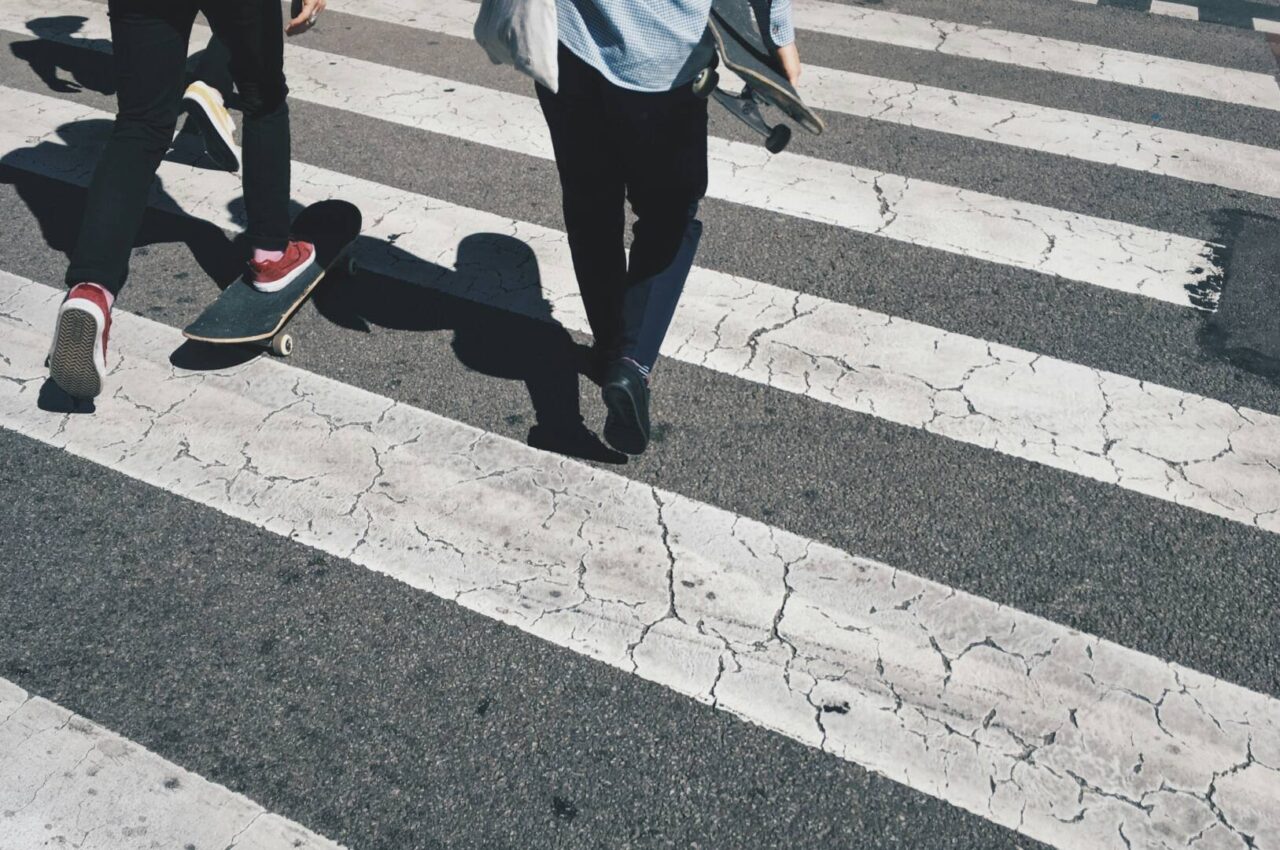
Removing Concrete: Precision and Power
The process of removing concrete typically requires heavy-duty machinery due to its hardness and density. Techniques such as diamond grinding, scarifying, and hydrodemolition are commonly employed.
- Diamond Grinding involves using a concrete grinder with a diamond-tipped blade to smooth or level the concrete surface. This method is precise and effective for removing coatings or minor surface imperfections.
- Scarifying uses a machine equipped with steel or carbide cutters to aggressively break up the concrete. It’s particularly useful for removing thicker coatings or leveling uneven surfaces but can leave a rough texture.
- Hydrodemolition utilizes high-pressure water jets to remove damaged concrete without affecting the structural integrity of the remaining surface. This method is selective and reduces the risk of microcracks in the remaining concrete.
Removing Asphalt: Managing Flexibility and Adhesion
Asphalt removal often demands a different set of techniques, primarily due to its flexibility and the sticky nature of bitumen. Methods like milling and cold planing are frequently used.
- Milling involves removing the top layer of asphalt with a rotary cutting drum, which can be adjusted to control the depth of cut. This method is ideal for removing worn-out asphalt or preparing the surface for resurfacing.
- Cold Planing is similar to milling but is used to remove deeper layers of asphalt. It’s effective for correcting surface irregularities or removing entire roadways in preparation for repaving.
Key Differences in Process
- Material Hardness: Concrete’s hardness requires more aggressive mechanical methods, while asphalt’s softer nature allows for easier removal but necessitates careful handling to prevent undue damage.
- Dust and Debris: Concrete grinding and scarifying produce significant dust, requiring dust extraction systems to maintain air quality. Asphalt milling generates less airborne dust but results in larger debris that must be collected and recycled.
- Surface Finish: Techniques used on concrete often aim for a smooth finish to ensure proper adhesion of new coatings. Asphalt removal, conversely, focuses on achieving an appropriate texture for subsequent layers of asphalt.
- Equipment Wear: Concrete’s density and abrasive properties can cause faster wear on cutting tools and blades, while asphalt’s stickiness and softer nature tend to clog and dull equipment more quickly.
Understanding these differences is crucial for choosing the most appropriate surface preparation technique, ensuring the longevity of the prepared surface, and optimizing the performance of the applied coatings or materials. By tailoring the approach to the unique characteristics of concrete and asphalt, professionals can achieve better results, extend the life of their equipment, and satisfy project requirements more effectively.
Back To Blog